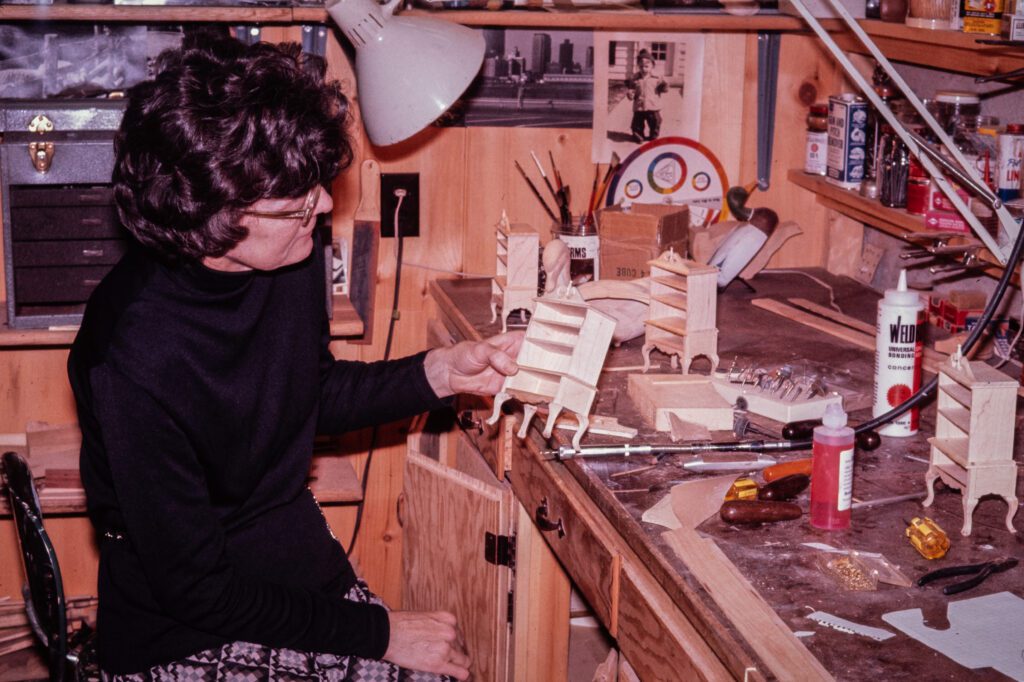
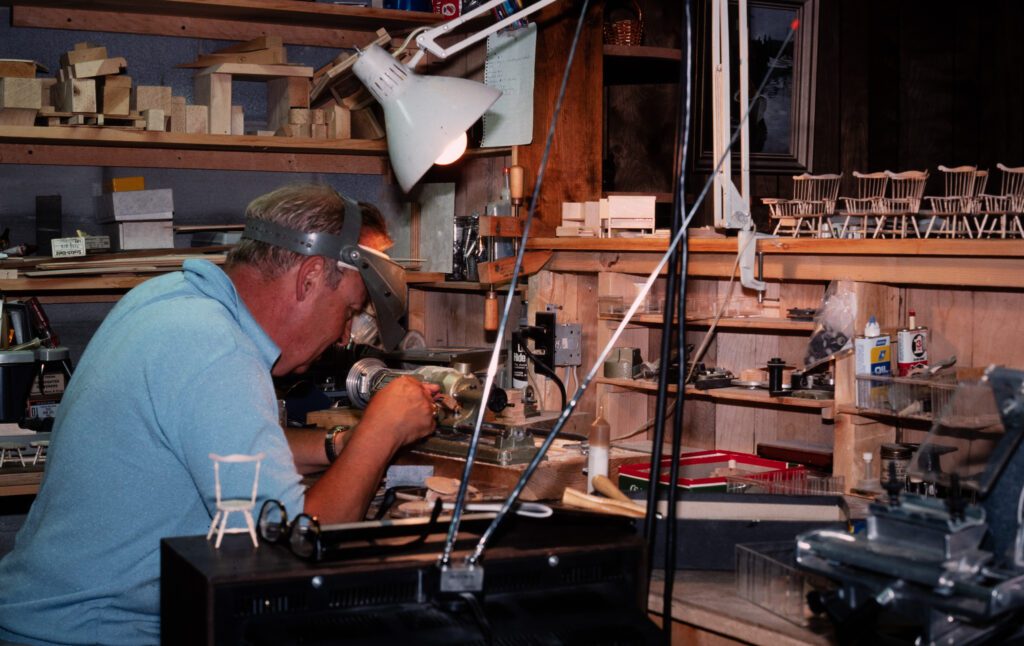
the woodwork
Bob Birkemeier always had a woodworking shop, something to work on and a new tool on his wish list. While miniatures are tiny, his experience turning a full size spinning wheel for daughter Wendy was invaluable when he started doing his miniature turnings. Of course the tools changed. Added were Unimat lathes, Foredom handpieces, jeweler saws and tiny dovetail machines. Magnifying lights and headpieces became invaluable. Millie Birkemeier did the finishing and provided quality control. Every chair and table received her once over, and didn’t leave the basement “factory” until it sat straight and square.
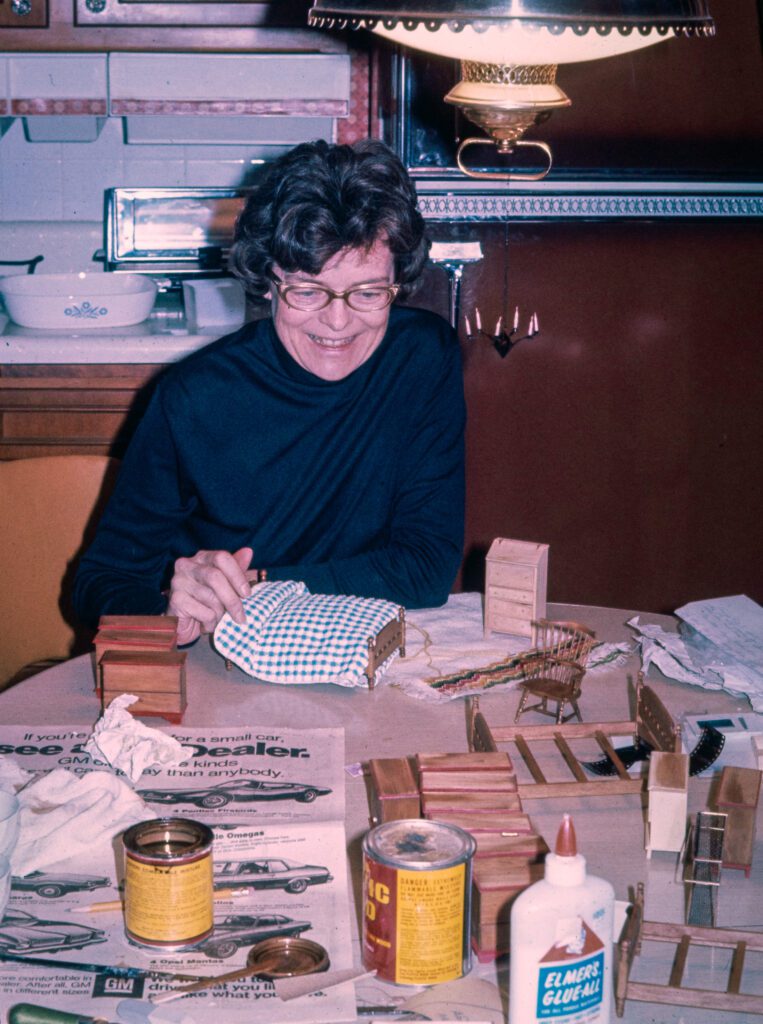

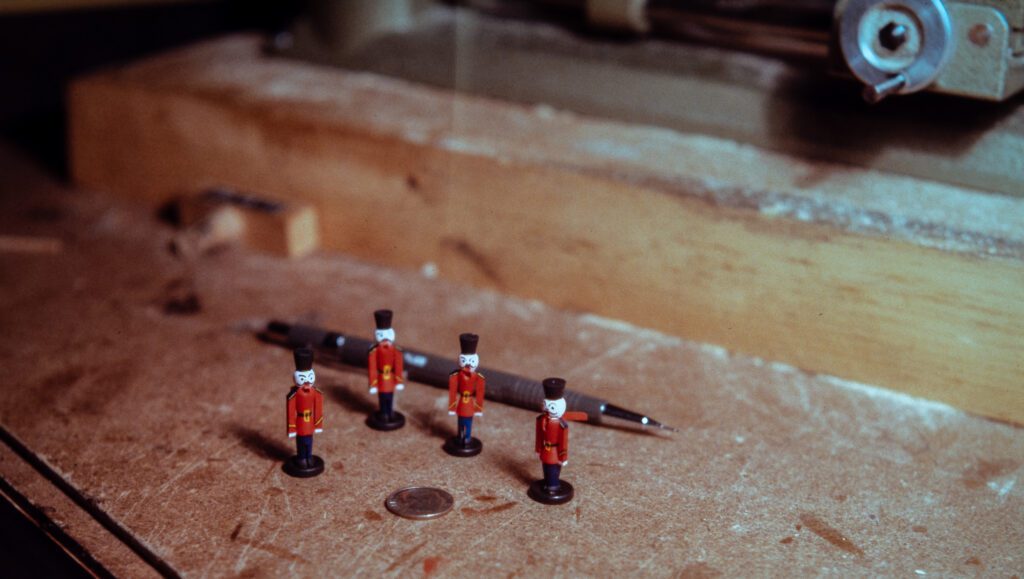
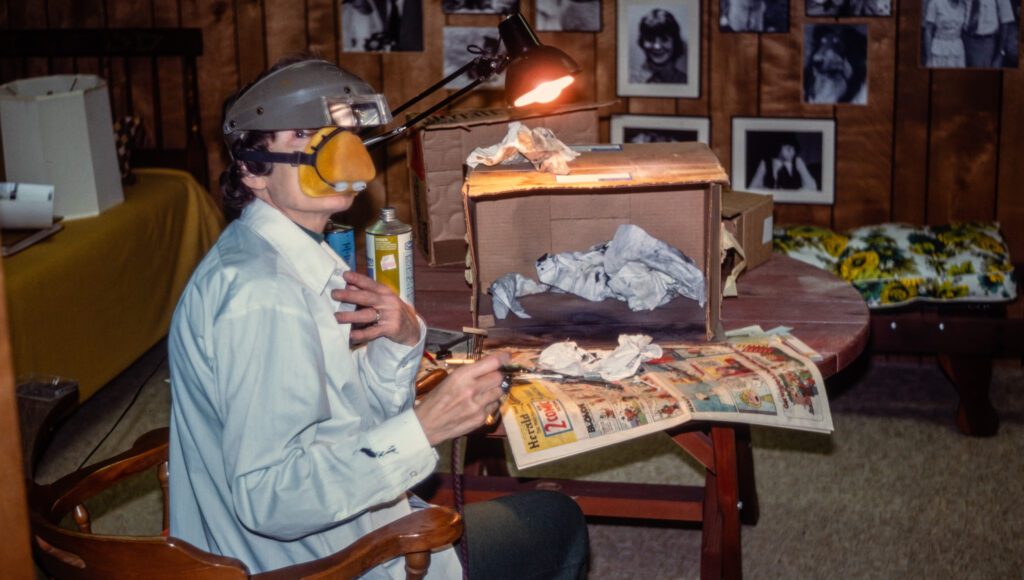
Studio B “burst” on the miniature scene when Bob and Millie entered a craft show in Connecticut with a number of early Windsor chairs and Boston Rockers at $25 a piece. After the show, another miniature craftsperson complemented them on the work, but suggested that they weren’t charging enough for their work. Of course that was not the intent – at that time, they had no idea what others charged for similar work. However, a Studio B trademark was a wonderful product at a reasonable price (typically what Millie would pay if she was buying!).
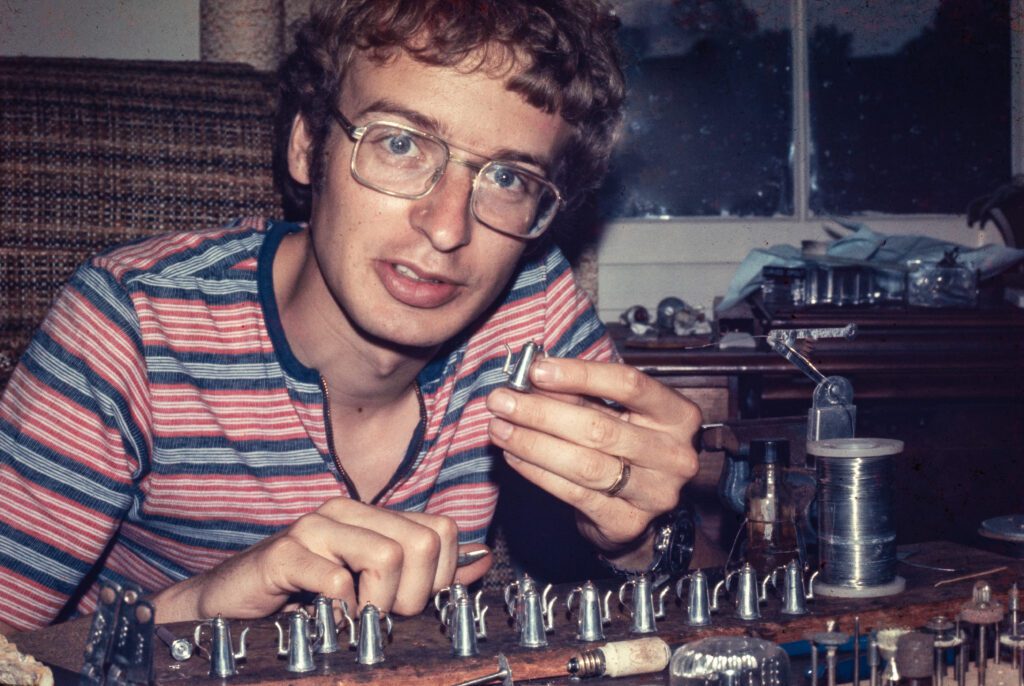
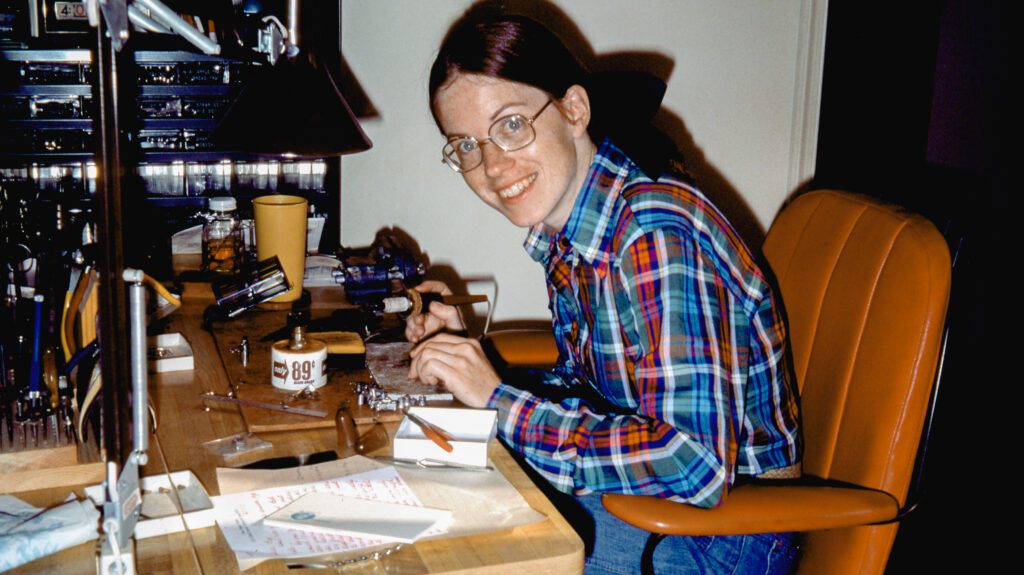
the tinwork
Bill and Peggy Birkemeier produced a wide variety of tinware pieces. Bill’s first piece was the punched tin lantern with no bottom, no door, no candle, and the top was punched in instead of out. Pretty rough. Fortunately the Miniature Shop in Hingham, MA raved about it anyway. With some proper tools and practice the pieces improved to the point that they looked correct in photographs blown up to be full size, complete with tiny hinges on the door.
Peggy transferred classic tole patterns to trays, mugs, creamers, coffee and tea pots, and adapted patterns to make matching sets of toleware that were custom ordered.
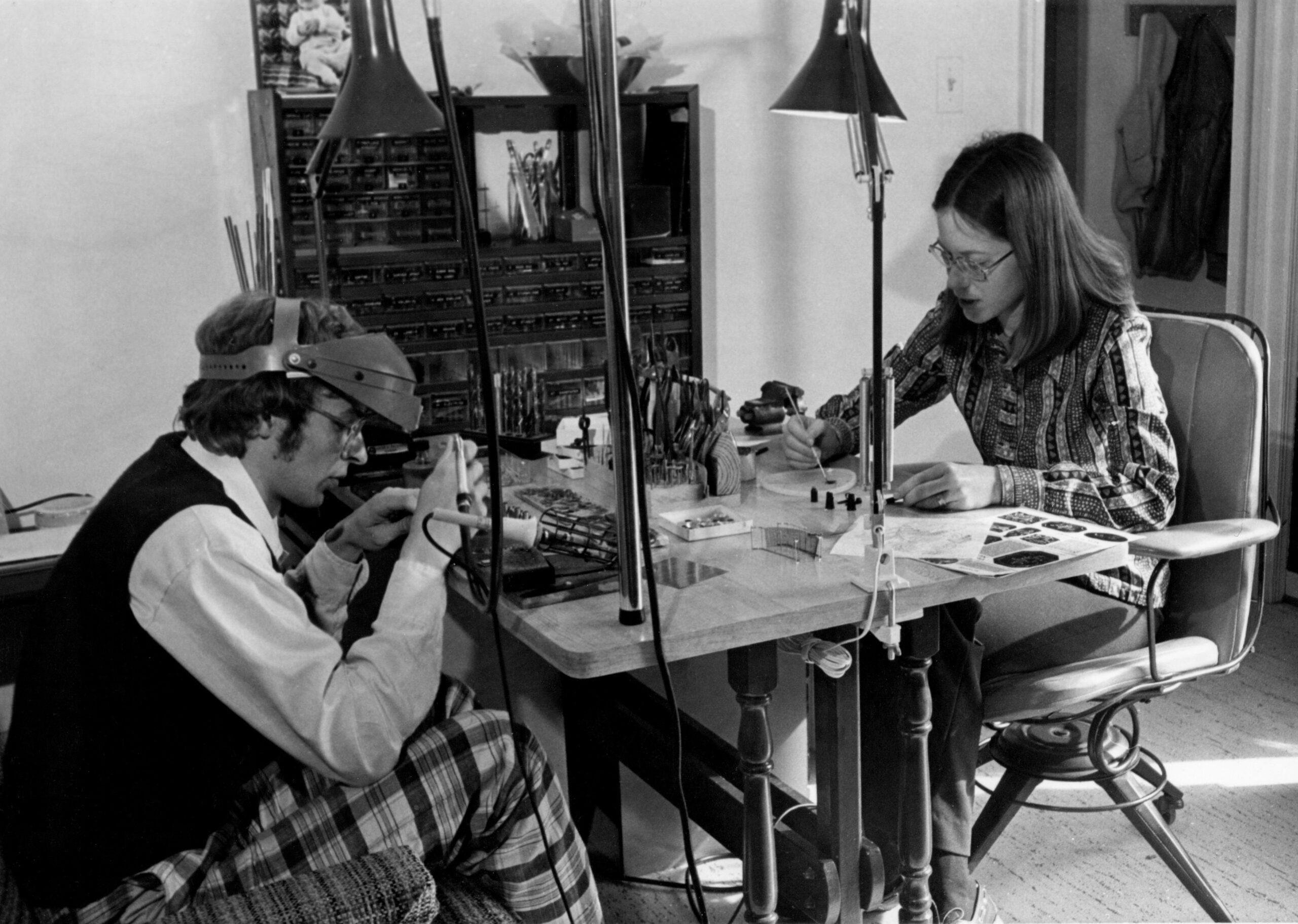
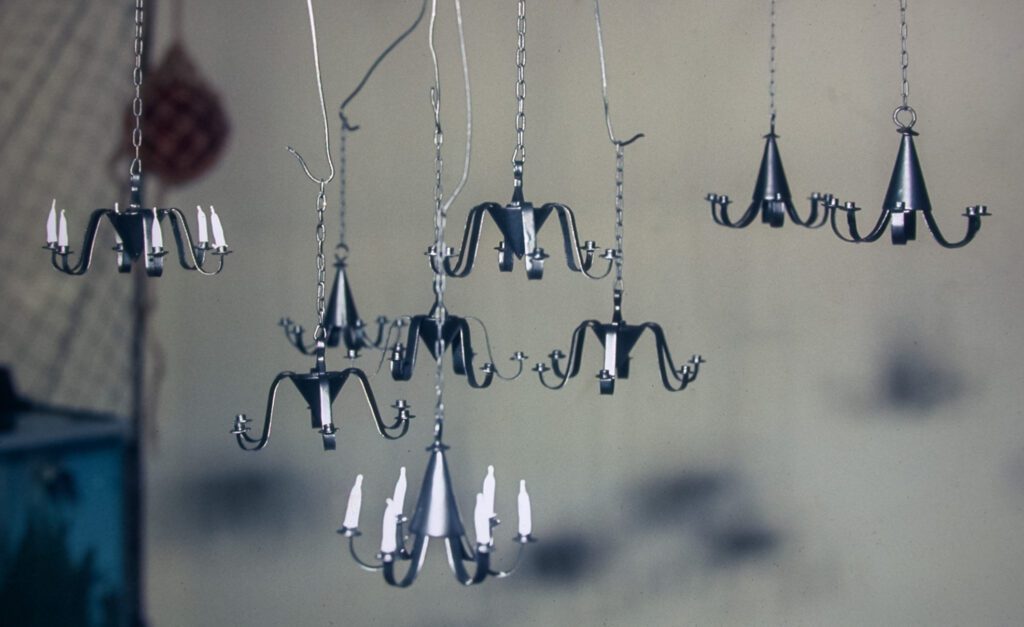
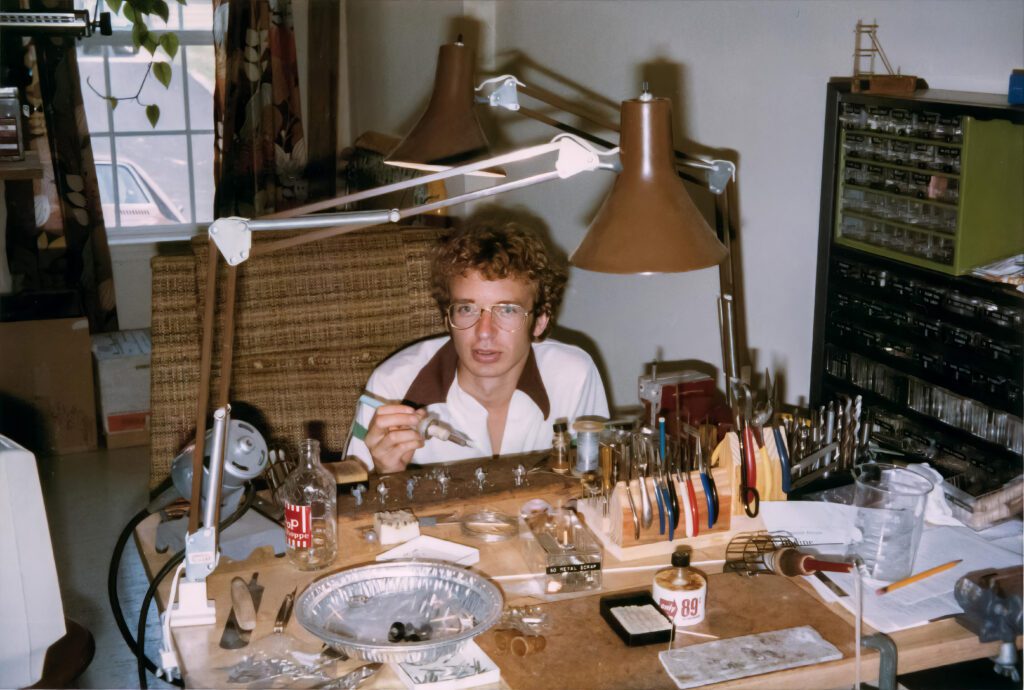
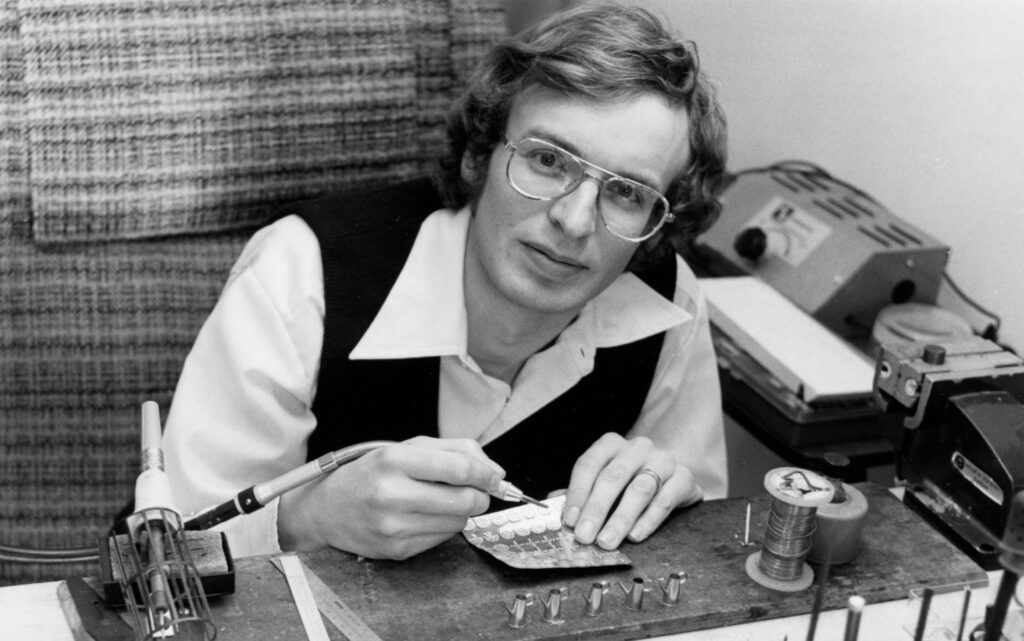
Candleholders need candles and Studio B’s first candles were threads glued to toothpicks that were repeatedly dipped, just as the colonists did. Needless to say, this was a slow process that did not create uniform, nor particularly nice candles. We still made and sold a lot. Imagine our surprise when we heard that one of our customers wanted to light them. Our nylon threads wouldn’t even burn. We switched to cotton, but have never thought it wise to light them around valuable miniatures – and the flame isn’t in scale. Our candlemaking process changed for good when we received an order for 450 sets of candles from the Metropolitan Museum of Art! That was too many to dip so Bill developed a mold and perfectly shaped candles (white, bayberry, and beeswax) could be made 24 at a time.
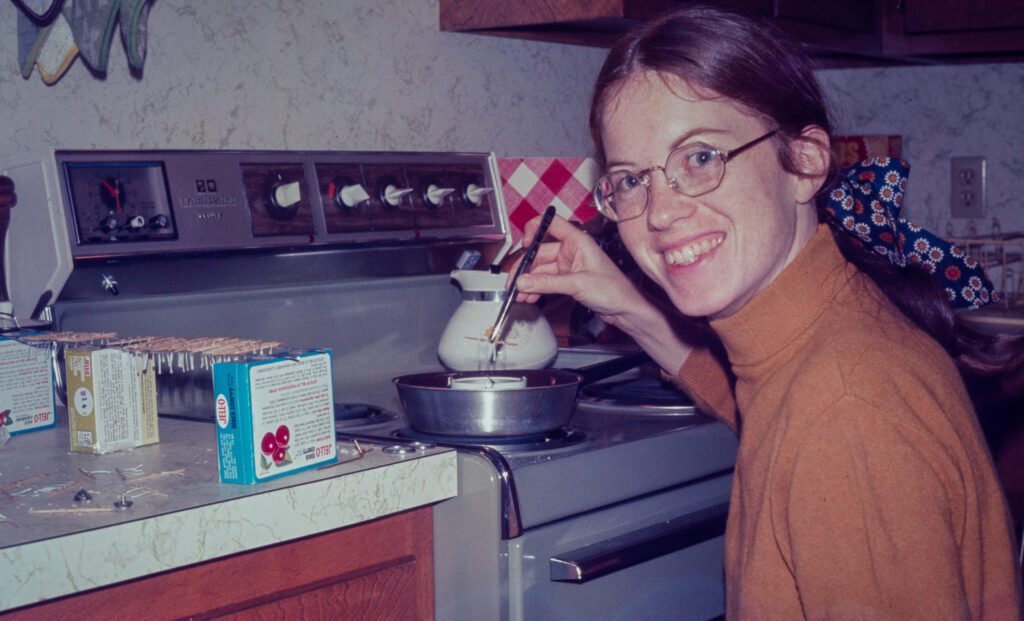
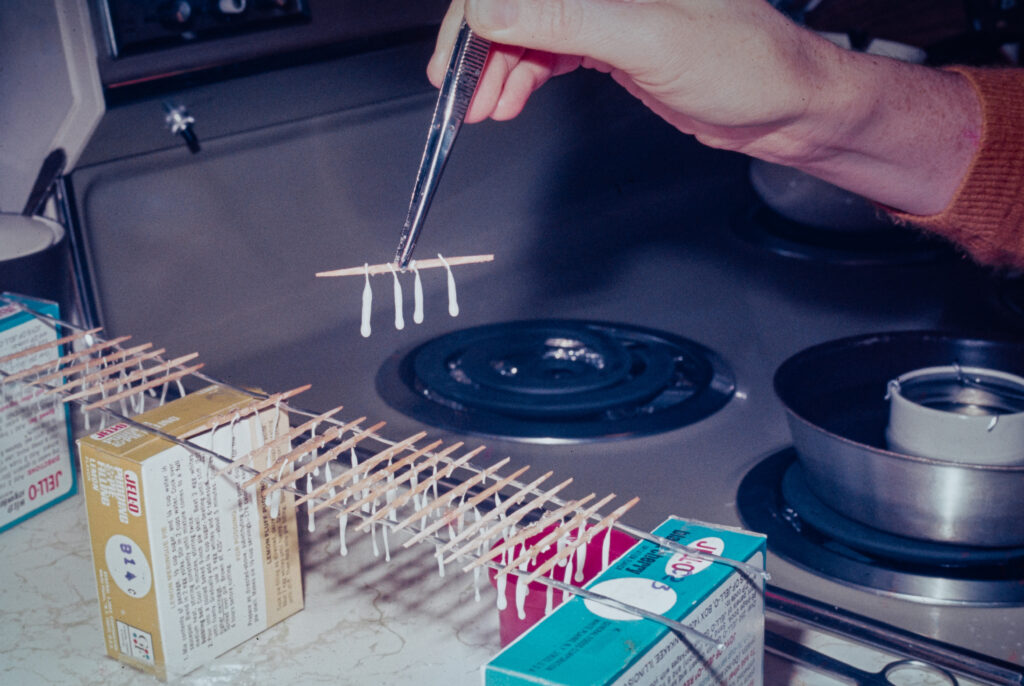